Ocean Insight’s Liquid Transmission Measurement System (LTMS) provides real-time, in-line monitoring of liquid colouring and coating applications used across the consumer electronics and food processing industries
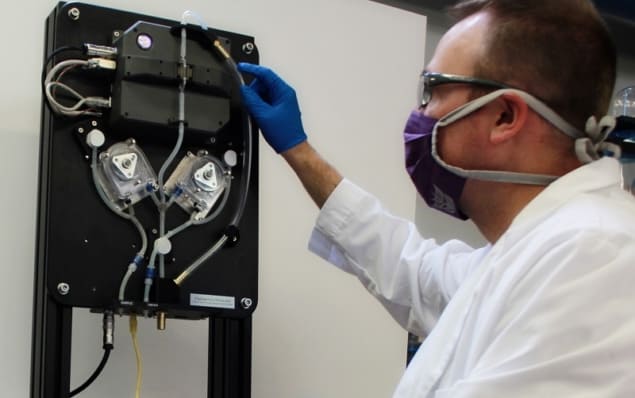
Ocean Insight, a US manufacturer of specialist spectral systems, software and optical solutions, has high hopes for its Liquid Transmission Measurement System (LTMS), a spectroscopy-based unit for real-time, in-line optical monitoring of liquid concentration levels in a range of industrial plating, colouring and coating applications.
The modular system comprises a rugged optical sensing platform – spectrometer, control unit and machine-learning software – within a compact benchtop configuration that’s suitable for day-to-day deployment into harsh industrial environments. As such, the LTMS is able to generate high-precision colour and concentration measurements from the factory floor on a 24/7 basis, with flow-cell set-up and automatic fluid handling or built-in cuvette holder.
Right now, the LTMS is being sold directly into industry end-users and, once tailored to the customer’s requirements, comes ready to use “out of the box” in the manufacturing facility. “Alternatively, if the end-user has a preferred OEM integrator, the LTMS can be incorporated as part of their existing ‘smart factory system’, with or without fluid-handling capability,” explains Scott Scargle, director of strategic markets at Ocean Insight.
Getting the priorities right
Despite a myriad of potential LTMS applications, Ocean Insight’s near-term focus for the product is in the consumer electronics and food processing industries. Colour consistency of external parts – for Bluetooth speakers, MP3 players and the like – is a major pain-point in the consumer electronics supply chain, with batch-to-batch consistency of anodized aluminium being notoriously difficult to control.
Anodization is an electrolytic process to create a protective, anti-corrosion layer on the aluminium surface – a coating that can subsequently be dyed and decorated in a range of colours. Trouble is, anodization chemistry remains something of a black art, with colour materials and finishing (CMF) designers and contract manufacturers forced to work with wide colour tolerances and complex production processes.
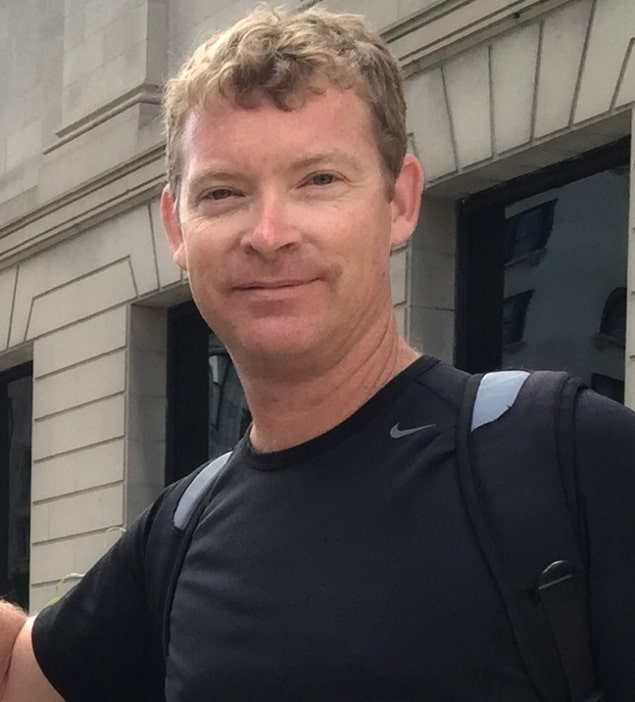
If that’s the problem, the LTMS looks a lot like the answer. With its ability to measure solution concentrations in the anodization tank out on the factory floor, those CMF tolerances can actually get a lot tighter – which translates into enhanced repeatability, less scrap and streamlined product development cycles. “In short,” notes Scargle, “the LTMS gives the CMF designers a wider colour palette to choose from, while the contract manufacturers can make their parts with better consistency.”
In the food-processing industry, meanwhile, the LTMS is being lined up to support specialist coating applications on a range of foodstuffs. A case in point is the wax coatings that packing-houses apply to citrus fruits – typically to prolong the shelf-life and enhance the visual appeal of the fruit, also to act as a carrier for antifungal agents. “It’s a balancing act,” says Scargle. “The LTMS can be used to make sure concentration levels are within a certain tolerance to meet health and safety requirements, while high enough to maintain a level of effectiveness.”
Another use-case is the application of pesticides to food crops. Before a pesticide mix is applied in the field, for example, the LTMS is able to verify that the concentration falls within a window of acceptance to meet statutory safety guidelines. “Equally important,” adds Scargle, “the LTMS can be used to check the rinse water after the pesticide storage tank is cleaned, ensuring there are no unwanted residuals left behind that may end up being sprayed on crops later.”
Benefits and efficiencies
When it comes to customer upside, one of the big advantages of the LTMS is in-line deployment – a feature that makes it possible to more readily address quality issues as they occur. Consider an aluminium anodization coating tank, the electrolytes of which need to be analysed versus pass/fail criteria on a regular basis. Traditionally that testing has relied on expensive analytical equipment – for example, high-performance liquid chromatography (HPLC) – in a central laboratory (or more often an offsite testing facility for smaller contract manufacturers).
All of which is time-consuming, manually intensive and can mean significant process downtime while the results are pending. “The LTMS essentially eliminates that whole walk-to-lab workflow,” says Lu Luo, sales director at Ocean Insight and head of the company’s development facility in Rochester, New York. “It’s about the benefits of real-time, in-line diagnostics – the workflow and resource efficiencies plus greater process uptime – versus manually intensive and centralized lab testing.” What’s more, the LTMS workflow is such that scientific staff are no longer tied up on routine quality-control tasks. “It’s a portable unit and can be operated from a user-friendly interface by a technician,” Luo adds.
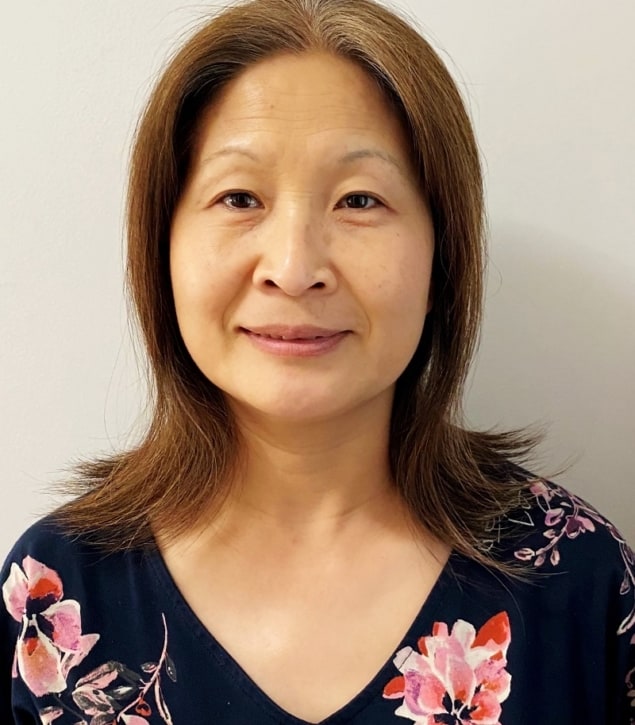
Another notable feature of the LTMS is the innovative use of machine-learning technology. Each customer gets a tailored system that’s “trained” for their specific optical sensing applications versus a number of chemical solutions. “The machine-learning models provide a direct answer on solution concentrations for pass–fail manufacturing decisions – either on the technician’s display or sent digitally to a central manufacturing execution system,” says Luo.
It’s a neat innovation that comes with in-built scalability. “Customers can step-and-repeat for different liquids and coating solutions, training new machine-learning models as they go and growing their database of models,” Luo adds.
Ultimately, the LTMS represents a further signal of intent from Ocean Insight as it seeks to reinforce its credentials as the “Applied Spectral Knowledge Company” across the photonics value chain – optical components, systems, software and industrial solutions. “We are a global optical solutions company – helping research customers to unlock new scientific insights and industry customers to deliver new commercial opportunities,” notes Scargle.
“Our scientists and engineers create value in all sorts of ways,” he concludes, “whether that’s feasibility testing through our lab services group; machine-learning advances from our Ocean Intelligence group; or custom product development in our solutions engineering team.”