Vacuum specialists are working closely with production engineers to make lithium-ion battery manufacturing more efficient – reducing costs and cutting carbon emissions, as Susan Curtis reports
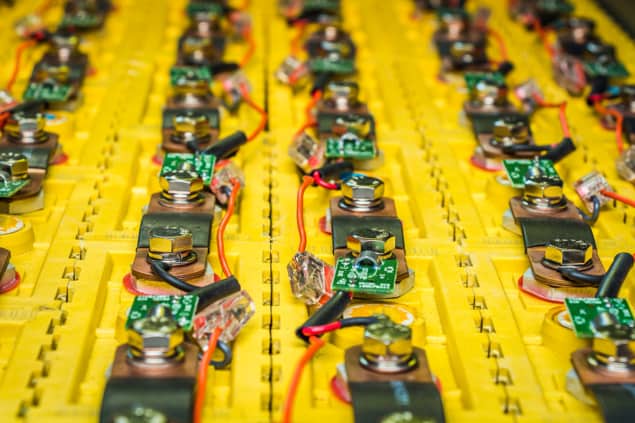
Together with government initiatives to reduce our reliance on fossil fuels, these developments are expected to drive a rapid rise in sales of fully electric vehicles. China’s government has made electric transport a national priority, while generous incentives in Norway have persuaded around half of Norwegian drivers to buy electric. What’s more, 13 major economies, including the UK, Japan and Germany, have pledged to increase the market share for electric vehicles to 30% of all new car sales by 2030. If that happens, the International Energy Association predicts in its 2021 Global EV Outlook that more than 250 million electric vehicles will be on the roads by 2030 – around 15% of the global fleet – with annual sales reaching 44 million per year.
Mass adoption of electric vehicles will, however, require rapid expansion in manufacturing capacity for lithium-ion batteries. In a detailed technology roadmap, the German Association for Mechanical Engineering (VDMA) estimates that current manufacturing facilities, most of which are located in China, produce batteries with a combined power output of a few hundred gigawatt-hours (GWh). By 2030, the VDMA predicts that demand will grow to almost 3000 GWh – and potentially double that, in in the most optimistic scenario. As a result, both established cell manufacturers and a clutch of newcomers have announced plans for new facilities, with a greater presence in the US and Europe to supply car producers in those regions.
But building new facilities won’t just be a case of replicating existing ones. The underlying technology is still in flux. Lithium-ion batteries are currently made in three different formats, each of which needs a slightly different approach. New materials and electrode designs continue to boost performance and lifetime. And while relatively little R&D effort has so far gone into optimizing battery production, that may be about to change. “There is a huge cost pressure on automotive batteries, which is dictating a move to larger facilities – so-called gigafactories – and more automated processes,” says Marc Locke, a battery production engineer at RWTH Aachen in Germany. “Another major focus is to improve sustainability, both through reducing the amount of wasted material and by developing more efficient production processes that will significantly reduce the carbon footprint of battery manufacture.”
Vacuum technologies have a major part to play in these improvements. Vacuum is already used in several stages of battery production, from the fabrication of the electrodes through to cell assembly, final finishing and test. In many of these steps, vacuum systems work to eliminate contaminants and remove residual moisture, improving the quality and performance of the battery while avoiding wastage.
In the first stage of battery production, active electrode materials are mixed in a slurry with binding agents and solvents. Most mixers operate under vacuum to prevent particulate ingress and avoid the formation of air bubbles, improving both the purity and the homogeneity of the paste.
Later, after the slurry has been processed and formed into electrodes, vacuum drying is used to remove all traces of moisture and solvents from the structure. Combining heat with vacuum speeds up evaporation and reduces the required temperatures, making drying more efficient. The vacuum environment is critical for producing high-quality electrodes, says Sina Forster, product manager for industrial vacuum at Leybold. “To maintain purity, oil-free vacuum pumps are deployed to ensure that no oil particles from the pump can get into the drying chamber and degrade the electrode,” she says.
Vacuum technology is also crucial when the assembled battery cells are filled with electrolyte and the finished battery is degassed. Here, high-quality vacuum maintains safety as well as preventing contamination, as the electrolytes are toxic and highly flammable. Dry-running pumps have become the most popular option at this stage since they can handle toxic gases without the need for pump oil and filters that would otherwise need frequent changing.
Despite the advantages vacuum technology brings, there is still room to improve efficiency
Greening the vacuum
Despite the advantages vacuum technology brings, there is still room to improve the efficiency of these production processes. Vacuum drying, for example, is both time consuming and energy intensive, requiring electrodes to be heated under vacuum for 12–30 hours. Indeed, an analysis in 2017 by Chris Yuan and colleagues at Case Western Reserve University in the US suggests that vacuum drying accounts for 47% of the total energy needed to manufacture the battery pack for a Nissan Leaf.
Adding infrared lamps can speed up the process, as can more powerful vacuum pumps. “The performance of the pumps has a direct influence on the process times, since in battery cell production we usually have big installations with high volumes,” Forster says. “In vacuum drying, for example, pumps usually offer pumping speeds of around 500 m³/h – like our DRYVAC DV650 – often with an additional booster.”
While the pumps themselves account for only a small part of the energy used in vacuum drying, Forster says that Leybold is nevertheless seeking more energy efficient solutions, both through hardware changes and by introducing systems that only provide vacuum when it’s needed. “Typically, vacuum pumps always run at full speed, even though the required vacuum level might change during a process cycle,” Forster explains. “Intelligent pumps can achieve significant energy savings by only providing the pumping speed that is required.”
Production engineers would also like to replace conventional batch drying methods – in which the electrodes are loaded into an oven and the pressure and temperature are changed until all traces of moisture have been removed – with a continuous version in which the electrodes move through a series of chambers with different environmental conditions. “It’s quicker and cheaper, and uses much less energy, but to be used in an industrial setting we still need better shutters and better insulation between the chambers,” Locke says.
In the longer term, Locke says that the goal is to replace the wet slurry currently used to mix electrode materials with a dry mixing and coating process. That would avoid the need for vacuum drying altogether, while also eliminating an earlier drying step in which a layer of the wet slurry is passed through a convection oven up to 80 m long. “Dry coating is the best solution both for cost and for energy consumption,” he says. “A great deal of research effort is focused on developing these dry processes, but no practical solution has yet been established.”
Filling the battery with electrolyte is another efficiency bottleneck. It’s a complicated process, as the highly porous structure of the electrode must be fully wetted for the battery to function properly. Using vacuum reduces filling times because it makes the process more precise, and because capillary forces help draw the electrolyte into electrode structure. However, this filling and wetting process must often be repeated several times – and each time the pressure must be cycled between normal atmospheric pressure and vacuum levels of 100–300 mbar.
Engineers are investigating ways to speed up this filling and wetting process. One option is to optimize the configuration of the cell to enable more efficient wetting. Another is to pre-treat the inert elements of the cell – which tend to be made from hydrophobic polymer materials – to enable them to soak up the electrolyte more quickly. Locke and his team are also developing measurement technologies based on electrochemical impedance spectroscopy (EIS) to enable real-time monitoring of the wetting process. “The EIS measurement can tell us if the filling and wetting process is complete, or whether we need to add more electrolyte or apply a lower pressure,” he says.
Industries join forces to power up electric vehicles
More generally, greater efficiencies could be achieved by replacing the individual batch processes that dominate battery manufacture with a more continuous approach. Processes that require vacuum would then need to be seamlessly connected to other production steps – which again is driving a trend towards greater use of software. “More intelligent pumps can communicate with other process steps and manufacturing equipment to help increase throughput,” Forster explains. This joined-up approach could also reduce the need for clean and dry conditions throughout electrode production and cell assembly – which accounts for 30% of energy consumption according to the analysis by Yuan and colleagues – by replacing a single large, conditioned room with a series of so-called glove boxes or mini-environments.
Further advances in battery materials and design may also impact the production plants of the future. As well as new material chemistries, researchers are also pursuing alternative, solid-state battery designs that avoid liquid electrolytes altogether. “From our standpoint it is essential to keep up with market trends and technology developments,” Forster observes. “Only then can we estimate the impact on the vacuum demand and develop new solutions if necessary.”