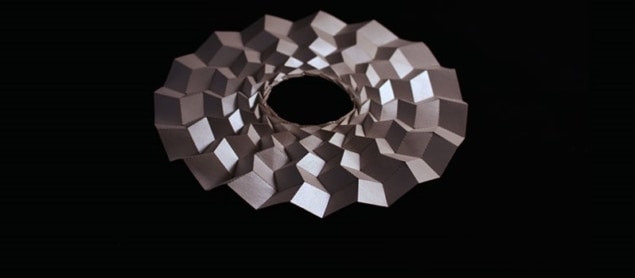
New research shows that microscale robots can be made from shape shifting 2D sheets. Itai Cohen and Itay Griniasty of Cornell University in the US have developed a mathematical technique for encoding the motion cycle of a tiny robot onto the surface of a flat material. Working alongside Cyrus Mostajeran of the UK’s University of Cambridge, they believe that their work will make it possible to design microscale swimming robots from materials such as liquid crystal elastomers and hydrogels.
Cohen is confident that microscale robots will one day perform many of the same tasks as their macroscale counterparts. He believes however, that at the micro and nanoscale, “We have to completely reimagine the way that we make machines”.
“The way that we’re going to do it is we’re going to manufacture everything in 2D and then release it from the substrate and get it to fold or assemble itself into some 3D object that can then do work on its environment.”
Microscale manufacturing challenges
Liquid crystal elastomer (LCE) sheets are a leading candidate for making microscale soft robots in this way. These flat materials deform into 3D shapes in response to light, heat and electromagnetic fields, with the initial alignment of the molecules determining the final curvature.
Designing functional machines from these sheets however remains a challenge. To perform useful work such as swimming, a robot needs to have more than one deformation programmed into it when it is manufactured. As an example, Cohen suggests a robot where some molecules respond to blue light and some to red light. However, the deformations would be coupled together, making it incredibly difficult to predict the final shape.
A mathematical solution
Griniasty joined the Cohen lab as a postdoc, bringing with him a mathematical technique that he, Cohen and Mostajeran have adapted to make their breakthrough. Griniasty had been using differential geometry to reverse engineer LCE- type sheets that deform into a single target shape. He predicted that the same method could be applied to a much more complex system, one where he was designing a robot that could deform into all the shapes in its motion cycle depending on the stimulus.
Researchers have experimented with origami-like sheets that fold into multiple shapes, but Cohen says that the advance in this latest work, “is the ability to form multiple shapes without going back the initial flat state… and that’s what opens up being able to do work and locomotion”.
The researchers found that in most cases, this theoretical technique could find an analytical solution; an alignment pattern that should cycle through an entire sequence of target shapes when deformed. They demonstrate as an example, a sheet that deforms first into a sphere, then a wavy pattern, and finally a face (see above figure).
Microswimmers manipulate single particles and cells
As proof of concept, they also propose a simple microswimmer that can move through a viscous fluid. The swimmer is a flat LCE type disk made up of two layers with orthogonal molecule alignments. When the layers are stimulated one after the other and then relaxed, the swimmer exhibits a cycle of conical and flat shapes, which the researchers predict will allow it to move through a fluid.
Whilst they have yet to test their theories in the lab, the team is optimistic about the results. As well as LCEs, they are investigating experimental realizations in inflatable and kirigami (cut and folded) sheets. The team has also released a software package that allows researchers worldwide to design shape shifting robots using their theory.
The research is described in Physical Review Letters.