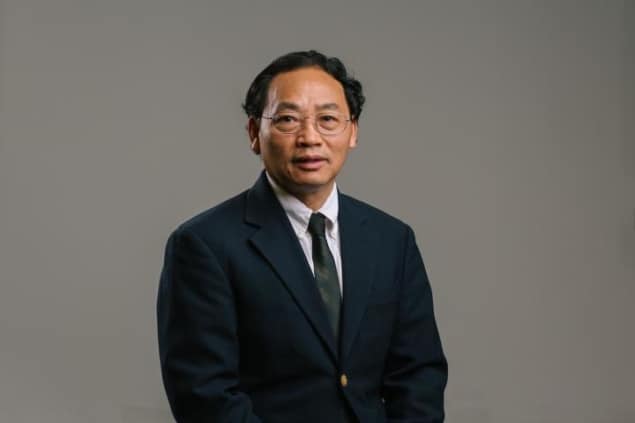
With the world’s reserves of light oil diminishing, oil companies are increasingly turning to heavier varieties – which make up 70% of global oil reserves – to meet rising energy demands. Existing extraction technologies for heavy oil are, however, inefficient, expensive and damaging to the environment in ways that extend beyond the CO2 emissions produced when the oil is eventually burned. A team of researchers from the University of Houston in the US have now developed an alternative method that uses an inexpensive, non-toxic sodium-based nanofluid to extract heavy oil from reservoirs, with an efficiency of 80% in laboratory tests.
Reserves of heavy oil – so-called because it has a viscosity of more than 100 centipoise, or cP – and extra-heavy oil, with a viscosity of more than 10 000 cP, are currently being exploited in several areas, notably Canada and Venezuela. The high viscosities of these grades of oils make them difficult to recover, and two main technologies are currently used to do it. The first relies on extracting oil from surface sands using hot water and air bubbles, then diluting it with solvents such as n-pentane or n-heptane. This method has been used for decades, but it requires large quantities of water and is thus not suitable for all locations.
Since most heavy oil resources are located below the surface, the second, in situ, recovery method is more common. In recent years, researchers have developed both thermal and non-thermal variants of these in situ techniques. The former, which include cold production with sands, vapour extraction, chemical injection and “flooding” the oil with steam, can be used for thin layers of oil formations. The problem is that these techniques are limited to shallow layers and relatively light (< 200 cP) viscous oils.
Alternative techniques sought
While thermal methods like in-situ combustion and steam flooding can recover oil with higher viscosities (potentially more than 70%), they are only economically viable when oil formations are thick. Producing the steam they require also consumes fuel such as natural gas, leading to additional CO2 emissions.
To overcome these challenges, researchers have begun to explore alternative techniques, including some that use nanomaterials. Such approaches are not yet mainstream, and so far the nanomaterials developed have only played a secondary role – for example, modifying the flow behaviour (rheology) of crude oil or being used as catalysts to upgrade crude oil during steaming processes.
80% recovery efficiency
A team led by Zhifeng Ren, who is director of the Texas Center for Superconductivity at the University of Houston (TcSUH), has now used a sodium (Na) nanofluid to recover over 80% of extra-heavy oil (with a viscosity of over 400 000 cP) from sand packs in a laboratory experiment. The researchers made this nanofluid by using a hand-held blender to mix commercially-available bulk sodium chunks with silicone oil. This non-reactive solvent is necessary because (as we all remember from chemistry classes at school) sodium reacts very strongly when it comes into contact with water.
When the researchers do add water to their sodium nanofluid, it reacts according to the formula 2Na + 2H20 –> 2NaOH + H2. The substantial amount of heat produced in this reaction generates steam, which then reduces the viscosity of the heavy oil in a way that is similar to older steam flooding techniques – with the advantage that the sodium reaction is relatively easy to control and can be kick-started in situ simply by adding water. The sodium nanomaterials also dissipate once the reaction is complete, which means that the oil is not damaged by adsorbing the sodium. Finally, the technique does not use any fossil fuels to generate steam or hot water, thereby reducing the direct CO2 emissions from the oil-extraction process.
How do oil companies see the energy future?
“Based on these advantages, we anticipate that the sodium nanofluid could become a game-changing technology for recovery of oil of any viscosity, as well as a milestone in using nanotechnology to solve oil-recovery problems in the petroleum industry,” Ren and colleagues say.
Side benefits
The researchers note that by mixing their sodium nanoparticles in silicone oil, the particles dispersed throughout the simulated reservoir before coming into contact with water. This dispersion has the effect of triggering smaller chemical reactions across a larger area. The team says it may also be possible to disperse the sodium nanoparticles in other solvents, such as pentane and kerosene, or even to mix them with polymers or surfactants for a higher oil recovery rate.
As a final benefit, the researchers note that one of their reaction’s products, NaOH (sodium hydroxide), is routinely employed in oil fields to spark a different reaction that also reduces oil viscosity – a technique known as alkaline flooding. The other reaction product, H2, could be used for gas flooding – another common oil recovery technique – as well as for upgrading the heavy oil via a hydrogenation reaction.
The new technique is detailed in Materials Today Physics.